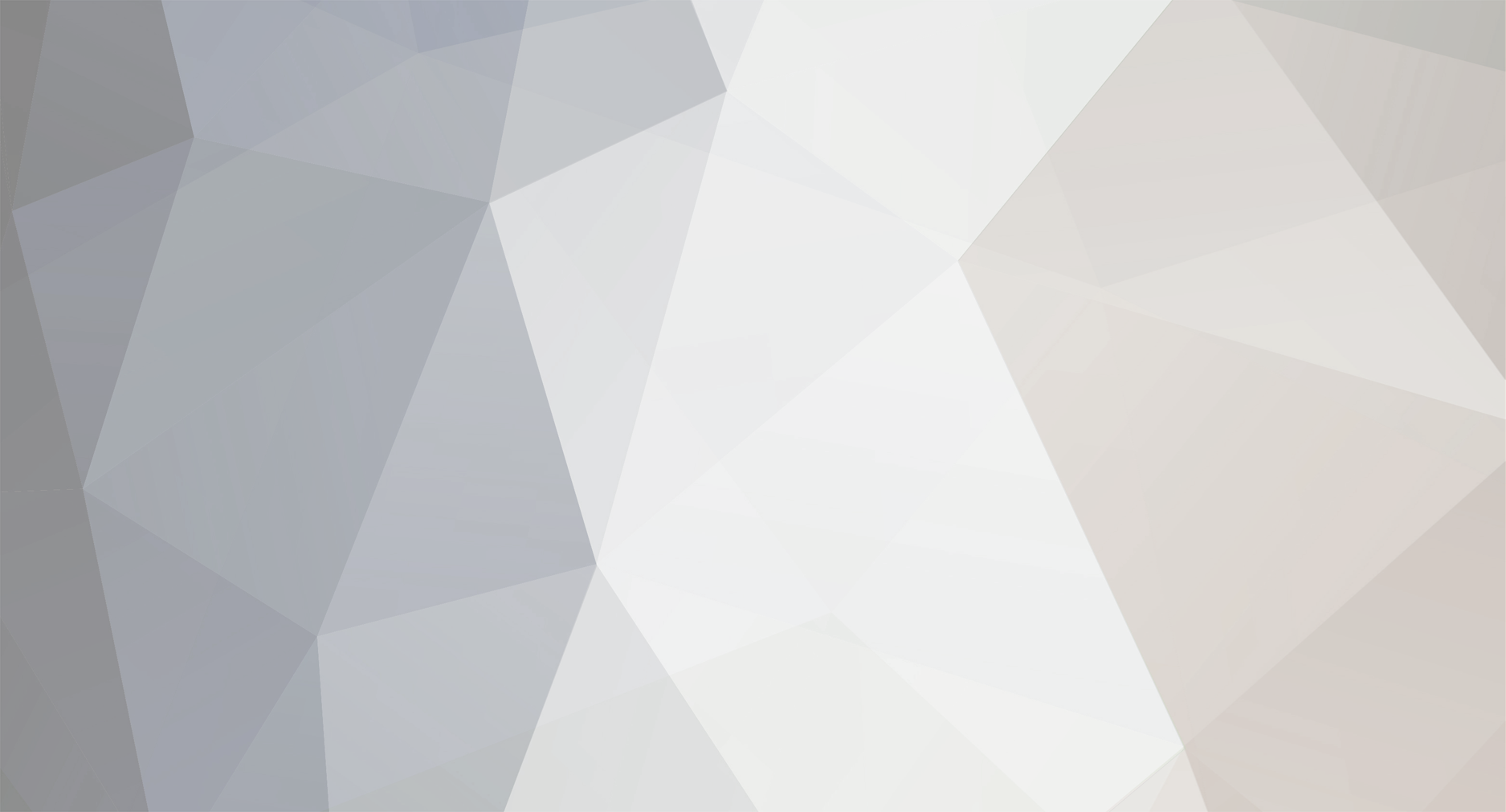
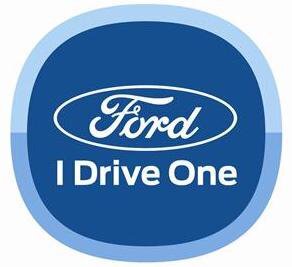
Haz
Edge Member-
Posts
1,515 -
Joined
-
Last visited
-
Days Won
407
Content Type
Profiles
Forums
Gallery
Everything posted by Haz
-
RDU Motor Actuator, failure advice? Part number?
Haz replied to Gnerffed's topic in Brakes, Chassis & Suspension
Additional supporting documents... ALL WHEEL DRIVE (AWD) MODULE - Connector C3841 Location UNDER VEHICLE Beneath Right Rear Seat- 2020 Edge.pdf Wheel Bearing and Wheel Hub - AWD - Removal and Installation - 2020 Edge Workshop Manual.pdf Axle Assembly - Removal and Installation - 2020 Edge Workshop Manual.pdf Muffler and Tailpipe - Removal and Installation - 2020 Edge Workshop Manual.pdf Fuel System Pressure Release - 2020 Edge Workshop Manual.pdf Fuel Tank Draining - 2020 Edge Workshop Manual.pdf Fuel Tank - Removal and Installation - 2020 Edge Workshop Manual.pdf Differential Fluid Level Check - 2020 Edge Workshop Manual.pdf Rear Drive Unit (RDU) - Specifications - 2020 Edge Workshop Manual.pdf- 11 replies
-
- 3
-
-
- speed and position sensor
- rdu actuator motor
-
(and 2 more)
Tagged with:
-
RDU Motor Actuator, failure advice? Part number?
Haz replied to Gnerffed's topic in Brakes, Chassis & Suspension
Welcome to the Forum, @Gnerffed! The 2020 Edge Workshop Manual prescribes a specific Drive Cycle for diagnosis of Four-Wheel Drive concerns and it seemingly cautions against performing Pinpoint Testing unless the Drive Cycle elicits the Diagnostic Trouble Code (DTC)... Four-Wheel Drive Systems Diagnostics in this manual assume a certain skill level and knowledge of Ford-specific diagnostic practices. Inspection and Verification NOTE: For most AWD System DTCs to set, the AWD module must detect the fault on 2 consecutive trips. 1) Record and clear DTCs from the AWD module. 2) Accelerate the vehicle from 0-45 mph with light (10%) APP. 3) Maintain 45 mph for 10 seconds. 4) Gently slow to a stop. 5) Repeat steps 2-4. 6) Accelerate the vehicle from 0-45 mph with moderate (30%) APP. 7) Maintain 45 mph for 10 seconds. 😎 Gently slow to a stop. 9) Repeat steps 6-8. 10) Turn off ignition, wait 1 minute. 11) Repeat steps 2-9 or until an AWD fault message is displayed in the IPC . Whichever is sooner. 12) Retrieve continuous memory DTCs from the AWD module. If no DTCs are present, the concern may be intermittent. Do not perform a pinpoint test unless the concern is present. Attached below are all Wiring and Workshop Manual sections related to Rear Drive Unit (RDU), including diagnostic Pinpoint Tests, and removal and installation procedures for the RDU Actuator Motor, RDU Speed Sensor, and All Wheel Drive (AWD) Module. If you progress through diagnostic Pinpoint Test(s) and identify a faulty component, then I'll try to determine an appropriate part number. Additional documents will be attached to an immediately following post, due to Forum file attachment limitations. Good luck! Rear Drive Axle and Differential - System Operation and Component Description - 2020 Edge Workshop Manual.pdf Four-Wheel Drive Systems - System Operation and Component Description - 2020 Edge Workshop Manual.pdf Four-Wheel Drive Systems - Diagnosis and Testing - EDITED - Diagnostic Drive Cycle - 2020 Edge Workshop Manual.pdf Four-Wheel Drive Systems - Diagnosis and Testing - EDITED - RDU-only PPTs - 2020 Edge Workshop Manual.pdf RDU Actuator Motor & Speed Sensor to AWD Module - Wiring Diagram - 2020 Edge.pdf RDU Actuator Motor & Speed Sensor to AWD Module - Inline Connector C4001 Details - 2020 Edge.pdf Inline Connector C4001 Location - UNDER VEHICLE - 2020 Edge.pdf Rear Drive Unit (RDU) Actuator Motor - Connector C3396A Details - 2020 Edge.pdf Rear Drive Unit (RDU) Actuator Motor - Connector C3396A Location - 2020 Edge.pdf Rear Drive Unit (RDU) Speed Sensor - Connector C3396B Details - 2020 Edge.pdf Rear Drive Unit (RDU) Speed Sensor - Connector C3396B Location - 2020 Edge.pdf ALL WHEEL DRIVE (AWD) MODULE - Connector C3841 Details - 2020 Edge.pdf Rear Drive Unit (RDU) Actuator Motor - Removal and Installation - 2020 Edge Workshop Manual.pdf Rear Drive Unit (RDU) Speed Sensor - Removal and Installation - 2020 Edge Workshop Manual.pdf All-Wheel Drive (AWD) Module - Removal and Installation - 2020 Edge Workshop Manual.pdf- 11 replies
-
- 4
-
-
- speed and position sensor
- rdu actuator motor
-
(and 2 more)
Tagged with:
-
Welcome to the Forum, @Steven H.! As is usually the case, three-dimensionally, there's more to it than meets the eye... Looking to Ford's online parts-selling site, that part is included in a Lock Cylinder Repair Kit... Link to this FordParts web page Door Cylinder Repair Kit photo - from FordParts... As @dabangsta describes, from the 2021 Edge Workshop Manual, Door Lock Cylinder Removal and Installation procedure... Removal NOTE: LH side shown, RH side similar. Remove the grommet. Remove the lock cylinder door handle cover. Hold the front door handle open. Turn the release screw 8 turns. The handle will release around 6 to 6.5 turns. You must continue to the full 8 revolutions for installation. Remove the lock cylinder and the door handle cover assembly from the front door. Remove the door lock cylinder. Installation To install, reverse the removal procedure. The Door Lock Cylinder Removal and Installation procedure is attached below as a PDF document. Good luck! Door Lock Cylinder - Removal and Installation - 2021 Edge Workshop Manual.pdf
-
Sunroof auto close
Haz replied to Oldone88's topic in Glass, Lenses, Lighting, Mirrors, Sunroof (BAMR), Wipers
Welcome to the Forum @Oldone88! The operating description from the 2019 Edge Workshop Manual is comparable to the Owner's Manual and entirely consistent with @akirby's description... Switch and Control When the roof opening panel glass is in the fully closed position, pushing the roof opening panel control open switch will activate the one-touch open feature, first opening the roof opening panel shield if it is closed, then opening the roof opening panel glass. With the roof opening panel glass in any open position, pushing the roof opening panel control close switch will activate the one-touch close feature which will close the roof opening panel glass to approximately 12 in. (305 mm) from the closed position and then the switch must be held to full close. When in one-touch open or close mode, activating any roof opening panel control switch will cancel the one-touch operation and stop the glass movement. Near the end of forward travel while closing, the front of the roof opening panel glass moves downward into the cams. This allows a weather-tight seal when the roof opening panel glass is closed. The roof opening panel control switch has a separate roof opening panel shield open and close switches to operate the shield independent from the glass. The shield will not close if the glass is in the open position. When the roof opening panel glass is in the closed position, pushing the roof opening panel control switch tilt switch will open the roof opening panel sliding panel to the vent position. When the roof opening panel glass is in the vent position, pushing the roof opening panel close switch will close the roof opening panel glass. Good luck! Roof Opening Panel - System Operation and Component Description - 2019 Edge Workshop Manual.pdf -
What else does the audio control module control
Haz replied to Honey's topic in Audio, Backup, Navigation & SYNC
Welcome to to the Forum @Honey! Presuming it was a dealership or other reputable repair shop that did the control module work, contact them and return the Edge for them to restore those previously working features which are no longer operative. It's possible some electrical connector(s) not fully engaged. The repair facility may find Diagnostic Trouble Codes (DTCs) which indicate the problem(s) their efforts subsequently created. Good luck! -
Welcome to the Forum @Lets_Go_riding! From the 2013 Edge Workshop Manual... Pinpoint Test M: Navigation Is Inoperative Or Navigation Application Is Unresponsive Normal Operation The Global Positioning System Module (GPSM) provides information from the GPS satellite system to the Accessory Protocol Interface Module (APIM) . This information is used to calculate vehicle position and direction of travel. Removal of the navigation SD card results in loss of navigation while the card is removed. This is normal operation. DTC B1215:00 (External Memory Card: No Sub-Type Information) — set by the APIM when it detects a device conflict through the media hub, a fault in the USB cable or media hub, or there is no Secure Digital (SD) card present when the vehicle is equipped with navigation. This pinpoint test is intended to diagnose the following: Navigation map SD card not present Network communication concern Vehicle not equipped with factory-installed Navigation APIM GPSM Map data NOTE: Verify the key is in the ON position (navigation function may be limited in accessory mode on some vehicles). NOTE: Make sure the navigation Secure Digital (SD) card is present and fully seated in the Secure Digital (SD) card slot. NOTE: Make sure the vehicle is located in a clear, open area to ensure the satellite information can be received by the vehicle. PINPOINT TEST M : THE NAVIGATION IS INOPERATIVE OR NAVIGATION APPLICATION IS UNRESPONSIVE M1 DETERMINE IF THE VEHICLE IS EQUIPPED WITH A FACTORY-INSTALLED NAVIGATION SYSTEM Make sure the correct VIN was entered on the technician service publication website. Hover the mouse cursor over or click on the OASIS tab toward the top LH corner of the screen. Select HVBoM (Historical Vehicle Bill of Material). Enter the map data Secure Digital (SD) card base part number "19H449" (do not include quotation marks). Press Enter on the keyboard or click on "View BoM (Build of Material)". If the vehicle is equipped with a factory-installed navigation system, a row will appear indicating "CARD-MEMORY" in the DESCRIPTION column. If the vehicle is not equipped with a factory-installed navigation system, a row will not appear and the DESCRIPTION column will be blank. Does the technician service publication website indicate the vehicle is equipped with a factory-installed navigation system? Yes GO to M2. No Ford Motor Company does not support the addition of a navigation system to vehicles not equipped with a factory-installed navigation system. M2 CHECK THE FDIM TOUCHSCREEN RH UPPER TAB Ignition ON. Check the navigation status of the FDIM touchscreen RH upper tab with the vehicle running for at least one minute. Does the FDIM touchscreen RH upper tab read Navigation? Yes GO to M4. No GO to M3. M3 REPROGRAM THE APIM Perform the APIM Standard Programming. REFER to Accessory Protocol Interface Module (APIM) Standard Programming In this section. Override the Service Pack Installation and perform a Full Flash/Force CIP . Once the APIM programming is complete and the system has re-initialized, confirm that the RH upper tab of the FDIM touchscreen displays “NAVIGATION” and the navigation system operates correctly. Does the RH upper tab of the FDIM touchscreen display “NAVIGATION” and the navigation system operate correctly? Yes The concern was resolved by reflashing the APIM . The navigation system is operating correctly at this time. No GO to M4. M4 CHECK THE FDIM TOUCHSCREEN FOR SIGNS OF THE NO GPS SYMBOL Ignition ON. Look for the No GPS symbol to appear on the screen. Does the symbol appear on the screen? Yes GO to M6. No GO to M5. M5 CHECK FOR SCAN TOOL COMMUNICATION WITH THE APIM Ignition ON. Using a scan tool, perform the network test. Does the scan tool communicate with the APIM ? Yes GO to M7. No REFER to Section 418-00 The APIM Does Not Respond To The Scan Tool. M6 CHECK FOR GPSM COMMUNICATION WITH THE APIM Using a diagnostic scan tool, perform an APIM self-test. Are any DTCs recorded? Yes For DTC U016A:00, GO to Pinpoint Test W. For other DTCs , refer to Information and Entertainment System, DTC Chart: APIM . (Following this posted Pinpoint Test M, below...) No VERIFY the vehicle is located in a clear, open area to ensure the satellite Information can be received by the vehicle. DISCONNECT the battery for 5 minutes and RETEST the system for correct operation. If the concern is still present, and there are no DTCs recorded, GO to M9. M7 RETRIEVE THE DTCS FROM THE APIM NOTE: If DTC B1215:00 is set in the APIM and the RH upper tab of the FDIM , touchscreen displays “ SD CARD FAULT”. NOTE: If DTC U016A:00 is set in the APIM and the RH upper tab of the FDIM , touchscreen displays “NAVIGATION FAULT”. Using a scan tool, perform the APIM self-test. Are any DTCs present? Yes If DTC B1215:00 is present, GO to M8. If DTC U016A:00 is present, GO to Pinpoint Test W. For all others, refer to Information and Entertainment System, DTC Chart: APIM . No GO to M8. M8 VERIFY THE SECURE DIGITAL (SD) CARD WITH NAVIGATION MAP IS PRESENT AND FULLY SEATED NOTE: The Secure Digital (SD) card slot is spring loaded. To remove the Secure Digital (SD) card, push the card in and release it. Do not attempt to forcefully pull the card from the card slot. This may cause damage to the Secure Digital (SD) card. Check for the presence of a Secure Digital (SD) card with map data in the Secure Digital (SD) card slot of the media hub. Is the navigation map SD card present and fully seated? Yes GO to M9. No If a non-Ford supplied Secure Digital (SD) card is present, EXPLAIN to the customer that only a Ford supplied map data card will work with the Navigation system. If a Ford supplied Secure Digital (SD) card is present, REINSTALL the navigation map Secure Digital (SD) card and make sure it is fully seated. TEST the system for normal operation. M9 VERIFY OPERATION WITH A KNOWN GOOD SECURE DIGITAL (SD) CARD WITH NAVIGATION MAP NOTE: Refer to the Owner Guide for End Users License Agreement (EULA) for map content and content details. NOTE: The data on the existing Secure Digital (SD) card may contain inaccurate or incomplete information due to the passage of time, changing circumstances, sources used and the nature of collecting comprehensive geographic data, any of which may lead to incorrect results. Using a known good Secure Digital (SD) card with map navigation, attempt to use the navigation system. Does the navigation map operate correctly and is the Secure Digital (SD) fault not present? Yes GO to M10. No GO to Pinpoint Test H. M10 VERIFY SECURE DIGITAL (SD) CARD CONDITION Inspect the Secure Digital (SD) card for damage. Damaged Secure Digital (SD) card contact pins Damaged, bent or broken Secure Digital (SD) card case. Is any damage present? Yes INSTALL a new navigation Secure Digital (SD) card. No GO to M11. M11 RECHECK THE ORIGINAL SECURE DIGITAL (SD) CARD WITH NAVIGATION MAP REINSTALL the original Secure Digital (SD) card with map data into the Secure Digital (SD) slot of the media hub and attempt to use the navigation system. Does the navigation map operate correctly and is the Secure Digital (SD) fault not present? Yes The Secure Digital (SD) fault was due to an intermittent conductivity concern, or the Secure Digital (SD) was not fully seated in the card slot. The navigation system is operating correctly at this time. No GO to M12. M12 CHECK OPERATION OF NAVIGATION SYSTEM WITH MANUAL DESTINATION ENTRY NOTE: Dragging your finger and pinching two fingers will not scroll to a location or zoom in or out as in other devices on the market. Holding your finger on a location off-center will cause the map to scroll to that location. Refer to the Owner Guide for more information about navigating the map screen. Using the map feature, touch the screen at the requested destination. Verify there is a road present on the map at the requested location and verify the address of the destination is correct. Does the navigation system properly navigate to the destination requested? Yes GO to M13. No The information on the navigation Secure Digital (SD) card may not include the correct map data, or is in a different format than what was expected. The system is operating correctly at this time. NOTIFY the customer that there may be an updated map upgrade available for purchase. M13 RESET THE AUDIO SYSTEM MODULES AND RECHECK THE NAVIGATION SYSTEM OPERATION Disconnect the battery for 5 minutes, then reconnect it. Turn the infotainment system on and wait for the system to re-initialize. Operate the navigation system. Does the navigation system operate correctly? Yes The concern was resolved by resetting the audio system modules. The navigation system is operating correctly at this time. No GO to M14. M14 CHECK FOR CORRECT GPSM OPERATION Ignition OFF. Disconnect and inspect the GPSM connector. Repair: Corrosion (clean module pins or install new connectors or terminals) Damaged or bent pins (install new terminals or pins) Pushed-out pins (install new pins as necessary) Reconnect the GPSM connector. Make sure it seats and latches correctly. Operate the system and determine if the concern is still present. Is the concern still present? Yes CHECK OASIS for any applicable TSBs . If a TSB exists for this concern, DISCONTINUE this test and FOLLOW TSB instructions. If no TSBs address this concern, INSTALL a new GPSM . REFER to Global Positioning System Module (GPSM). If the concern is still present, GO to M15. No The system is operating correctly at this time. The concern may have been caused by module connections. ADDRESS the root cause of any connector or pin issues. M15 CHECK FOR CORRECT APIM OPERATION Ignition OFF. Disconnect the APIM connector. Check for: corrosion damaged pins pushed-out pins Connect the APIM connector and make sure it seats correctly. Wait 2 minutes for the APIM to re-initialize. Operate the system and verify the concern is still present. Is the concern still present? Yes CHECK OASIS for any applicable TSBs . If a TSB exists for this concern, DISCONTINUE this test and FOLLOW TSB instructions. If no TSBs address this concern, VIN required to access Guided Routine (APIM) No The system is operating correctly at this time. The concern may have been caused by a loose or corroded connector. ADDRESS the root cause of any connector or pin issues. If your diagnostic efforts reveal any of the following APIM Diagnostic Trouble Codes (DTCs) I can supply the indicated Pinpoint Test upon your request... Accessory Protocol Interface Module (APIM) DTC Chart — 4.2-Inch (107 mm) Screen SYNC® NOTE: This module utilizes a 5-character DTC followed by a 2-character failure-type code. The failure-type code provides information about specific fault conditions such as opens, or shorts to ground. CMDTCs have an additional 2-character DTC status code suffix to assist in determining DTC history. DTC Description Action B1252:04 USB Port: System Internal Failure GO to Pinpoint Test AI. B1252:11 USB Port: Circuit Short to Ground GO to Pinpoint Test AI. B12B8:04 USB # 2 Port: System Internal Failure NOTE: This DTC refers to USB port #2 on the APIM itself, which is not used. INSPECT the APIM USB port #2 for damage and remove any debris. CLEAR the DTCs . REPEAT the self-test. If DTC B12B8:04 is retrieved again, VIN required to access Guided Routine (APIM) B12B8:11 USB # 2 Port: Circuit Short to Ground NOTE: This DTC refers to USB port #2 on the APIM itself, which is not used. INSPECT the APIM USB port #2 for damage and remove any debris. CLEAR the DTCs . REPEAT the self-test. If DTC B12B8:11 is retrieved again, VIN required to access Guided Routine (APIM) B1D79:01 Microphone Input Circuit: General Electrical Failure GO to Pinpoint Test R. B1D79:11 Microphone Input Circuit: Circuit Short to Ground GO to Pinpoint Test R. B1D79:12 Microphone Input Circuit: Circuit Short to Battery GO to Pinpoint Test R. B1D79:13 Microphone Input Circuit: Circuit Open GO to Pinpoint Test R. U0140:00 Lost Communication With Body Control Module: No Sub Type Information GO to Pinpoint Test T. U0155:00 Lost Communication With Instrument Panel Cluster (IPC ) Control Module: No Sub Type Information GO to Pinpoint Test V. U0257 :00 Lost Communication With Front Controls/ Display Interface Module: No Sub Type Information GO to Pinpoint Test AC. U0423:00 Invalid Data Received From Instrument Panel Control Module: No Sub Type Information RETRIEVE and FOLLOW other DTCs present in the APIM or IPC . U2100:00 Initial Configuration Not Complete: No Sub Type Information REFER to Section 418-01. U2101:00 Initial Configuration Not Complete: No Sub Type Information REFER to Section 418-01. U3000:04 Control Module: System Internal Failure GO to Pinpoint Test AH. U3000:41 Control Module: General Checksum Failure CLEAR the DTCs . REPEAT the self-test. If DTC U3000:41 is still present, VIN required to access Guided Routine (APIM) U3000:42 Control Module: General Memory Failure CLEAR the DTCs . REPEAT the self-test. If DTC U3000:42 is still present, VIN required to access Guided Routine (APIM) U3000:88 Control Module: Bus Off REFER to Section 418-00. U3003:16 Battery Voltage: Circuit Voltage Below Threshold GO to Pinpoint Test AD. U3003:17 Battery Voltage: Circuit Voltage Above Threshold GO to Pinpoint Test AE. Additional 2013 Edge Workshop Manual resources... Good luck! Global Positioning System Module (GPSM) - Removal and Installation - 2013 Edge Workshop Manual.pdf Global Positioning System Module (GPSM) - Connector C2398 Location - 2013 Edge.pdf Accessory Protocol Interface Module (APIM) - Removal and Installation - 2013 Edge Workshop Manual.pdf Front Display Interface Module (FDIM) - Removal and Installation - 2013 Edge Workshop Manual.pdf Front Controls Interface Module (FCIM) - Removal and Installation - 2013 Edge Workshop Manual.pdf Console — Floor - Removal and Installation - 2013 Edge Workshop Manual.pdf
-
2017 EDGE TITANIUM STEERING BIND
Haz replied to dukester4413's topic in Brakes, Chassis & Suspension
Welcome to the Forum, @dukester4413! Slow-speed driver side clunk may be front strut upper bearing in need of replacement. If dealership work is not cause of the steering-snag symptom, per @omar302's concern, it could be the steering rack. If Edge is FWD, you could try putting the front end up on jack stands, to see if steering-snag symptom is present without weight bearing on the front suspension. Good luck! -
SSM 52432 2024 Nautilus - 2.0L EcoBoost-Hybrid - Fuel Injector Replacement On 2024 Nautilus 2.0L EcoBoost-Hybrid vehicles, if engine damage or drivability diagnosis leads to replacement of any fuel injector assemblies, replace all 4 fuel injector assemblies along with other necessary repairs. Refer to Workshop Manual, Section 303-04B. Engineering is currently investigating this concern. Monitor OASIS for further updates.
-
Sure enough, there it is, shown as "Included" in the Exterior section of Ford's 2024 Edge ST-Line Build & Price website... Good luck!
-
2007 Ford Edge horn not working
Haz replied to SD40-2's topic in Alarms, Keyless Entry, Locks & Remote Start
Welcome to the Forum, @SD40-2! From the 2007 Edge Wiring and Workshop Manuals... Good luck! Horn - Diagnosis and Testing - 2007 Edge Workshop Manual.pdf Horn - Removal and Installation - 2007 Edge Workshop Manual.pdf Horn - Connector C131 Location - 2007 Edge.pdf Horn - Power Distribution & SJB Wiring Diagram - 2007 Edge.pdf Horn - Steering Switches, Clockspring, SJB Wiring Diagram - 2007 Edge.pdf Horn - Grounds Wiring Diagram - 2007 Edge.pdf Horn - Ground G107 Location - 2007 Edge.pdf SMART JUNCTION BOX (SJB) - Connector C2280B Details - 2007 Edge.pdf SMART JUNCTION BOX (SJB) - Connector C2280E Details - 2007 Edge.pdf CLOCKSPRING - Connector C218A Details - 2007 Edge.pdf CLOCKSPRING - Connector C218A Location - 2007 Edge.pdf CLOCKSPRING - Connector C218B Details - 2007 Edge.pdf CLOCKSPRING - Connector C218B Location - 2007 Edge.pdf SMART JUNCTION BOX (SJB) - Various Connector Locations - 2007 Edge.pdf Horn Switch, Left - Connector C2996 Location - 2007 Edge.pdf Horn Switch, Right - Connector C2997 Location - 2007 Edge.pdf Driver Airbag - Removal and Installation - NOTE THE WARNINGS - 2007 Edge Workshop Manual.pdf Supplemental Restraint System (SRS) Depowering and Repowering - NOTE THE WARNINGS - 2007 Edge Workshop Manual.pdf Steering Wheel - Removal and Installation - 2007 Edge Workshop Manual.pdf Clockspring - Removal and Installation - 2007 Edge Workshop Manual.pdf Clockspring - Removal and Installation - ENHANCED IMAGE - 2007 Edge Workshop Manual.pdf SMART JUNCTION BOX (SJB) - Fuse-Circuit Legend - 2007 Edge.pdf -
The Workshop Manual procedure was revised in March 2016, and I'd say the Technical Writer's choice of "a speaker attached to the PAM" -- implying the speaker is physically fastened-to the PAM, or, fastened-upon the PAM -- is inaccurate. Better to say it's electrically connected to the PAM, or, wired to the PAM, since they are separate components, as shown in the online images you found and per garycrist's photos in his discussion. Good luck!
-
The Hands-Free Liftgate feature has generated a sufficient number of owner complaints to cause Ford to notify the Service community in February 2023 about the unintended-closure safeguard of keeping the keyfob away from the vehicle's backend when loading cargo. See Forum post SSM 51360 - 2021-2023 Edge Titanium/Nautilus - Unintended Hands-Free Liftgate Activation. And, while Edge/Nautilus is not specifically mentioned in this February 2024 message, Ford notified the Service community the Hands-Free Liftgate feature has been dropped from several other models... SSM 52269 Multiple Vehicle Lines - No Longer Equipped With A Hands Free Liftgate System 2022-2024 Explorer/Aviator vehicles built on or after 28-May-2022, 2022-2024 Expedition/Navigator vehicles built on or after 08-Jun-2022, 2022-2024 Escape vehicles built on or after 01-Jun-2022 and 2022 Corsair vehicles built on or after 01-Jun-2022 are no longer equipped with a hands free liftgate system. The vehicle is not misbuilt. The addition of any parts is not a warrantable repair. Do not submit a claim for this condition. And finally, the Feature Availability Guide for dealership personnel shows Liftgate variations, and Hands Free is shown as not available on the 2024 Edge ST-Line... Good luck!
-
Welcome to the Forum, @canucklehead! Regarding the park aid speaker, repair experience provided here by Forum member @garycrist may be helpful to you. The 2011 Edge Workshop Manual procedure and component depiction is consistent with the 2008 Edge documents and garycrist's findings. 2011 Edge Wiring and Workshop Manual sections relating to Parking Aid module & Sensor diagnostics and removal are attached below... Good luck! Parking Aid - Diagnosis and Testing - 2011 Edge Workshop Manual.pdf Bumper Cover, Rear - Removal and Installation - 2011 Edge Workshop Manual.pdf Parking Aid Sensor - Removal and Installation - 2011 Edge Workshop Manual.pdf Parking Aid Module - Removal and Installation - 2011 Edge Workshop Manual.pdf PARKING AID MODULE (PAM) - Connector C4014 Details - 2011 Edge.pdf PARKING AID MODULE (PAM) - Connector C4014 Location - 2011 Edge.pdf PARKING AID MODULE (PAM) and Sensors - Wiring Diagram - 2011 Edge.pdf PARKING AID MODULE (PAM) Power Distribution and Communications - Wiring Diagram - 2011 Edge.pdf Parking Aid Sensor - Connector Number Locations - 2011 Edge Workshop Manual.pdf PARKING AID SENSOR, OUTER LEFT - Connector C4009 Details - 2011 Edge.pdf PARKING AID SENSOR, INNER LEFT - Connector C4010 Details - 2011 Edge.pdf PARKING AID SENSOR, OUTER RIGHT- Connector C4011 Details - 2011 Edge.pdf PARKING AID SENSOR, INNER RIGHT - Connector C4012 Details - 2011 Edge.pdf
-
Welcome to the Forum @Harleyflt04! From the 2013 Edge Wiring Manual... Good luck! POWERTRAIN CONTROL MODULE (PCM) - Connector C175B Pin-Circuit Details - 3.5L TiVCT -2013 Edge.pdf POWERTRAIN CONTROL MODULE (PCM) - Connectors C175B, C175E, C175T Location in Bulkhead - 3.5L TiVCT -2013 Edge.pdf POWERTRAIN CONTROL MODULE (PCM) - Connector C175E Pin-Circuit Details - 3.5L TiVCT -2013 Edge.pdf POWERTRAIN CONTROL MODULE (PCM) - Connector C175T Pin-Circuit Details - 3.5L TiVCT -2013 Edge.pdf POWERTRAIN CONTROL MODULE (PCM) - Electronic Engine Controls #1 - 3.5L TiVCT -2013 Edge.pdf POWERTRAIN CONTROL MODULE (PCM) - Electronic Engine Controls #2 - 3.5L TiVCT -2013 Edge.pdf POWERTRAIN CONTROL MODULE (PCM) - Electronic Engine Controls #3 - 3.5L TiVCT -2013 Edge.pdf POWERTRAIN CONTROL MODULE (PCM) - Electronic Engine Controls #4 - 3.5L TiVCT -2013 Edge.pdf POWERTRAIN CONTROL MODULE (PCM) - Electronic Engine Controls #5 - 3.5L TiVCT -2013 Edge.pdf POWERTRAIN CONTROL MODULE (PCM) - Electronic Engine Controls #6 - 3.5L TiVCT -2013 Edge.pdf POWERTRAIN CONTROL MODULE (PCM) - Electronic Engine Controls #7 - 3.5L TiVCT -2013 Edge.pdf POWERTRAIN CONTROL MODULE (PCM) - Electronic Engine Controls #8 - 3.5L TiVCT -2013 Edge.pdf POWERTRAIN CONTROL MODULE (PCM) - Electronic Engine Controls #9 - 3.5L TiVCT -2013 Edge.pdf POWERTRAIN CONTROL MODULE (PCM) - Electronic Engine Controls #10 - 3.5L TiVCT -2013 Edge.pdf POWERTRAIN CONTROL MODULE (PCM) - Electronic Engine Controls #11 - 3.5L TiVCT -2013 Edge.pdf POWERTRAIN CONTROL MODULE (PCM) - Electronic Engine Controls #12 - 3.5L TiVCT -2013 Edge.pdf POWERTRAIN CONTROL MODULE (PCM) - Transmission Controls #1 - 3.5L TiVCT -2013 Edge.pdf POWERTRAIN CONTROL MODULE (PCM) - Transmission Controls #2 - 3.5L TiVCT -2013 Edge.pdf
-
SSM 52419 Various Vehicles - 1.5L/2.0L/2.3L - Misfire With Diagnostic Trouble Code (DTC) P0301, P0302, P0303, And/Or P0304 Stored In The PCM Some 2023-2024 Escape/Corsair vehicles equipped with a 1.5L or 2.0L EcoBoost engine, 2024 Mustang vehicles equipped with a 2.3L EcoBoost engine, and 2024 Nautilus vehicles may exhibit an engine misfire condition with diagnostic trouble codes (DTC) P0301, P0302, P0303 and/or P0304 set in the powertrain control module (PCM). If the codes are stored in the PCM, remove and inspect the condition of all the spark plugs. If any spark plugs appear to be damaged, use a borescope to inspect the condition of the cylinder walls. If the cylinder walls are scored/scraped/damaged, replace the long block engine assembly (6006) to resolve this condition. If the cylinder walls are not scored/scraped/damaged, replace the damaged spark plug(s) and advise the customer that engineering is investigating this issue. Monitor OASIS for additional information and schedule service appointments for customers once the repair becomes available.
-
Two terminal versus three terminal oil pressure switch/ sensor
Haz replied to JayMarks40's topic in 2015 Edge & MKX
DIAGNOSTIC PINPOINT TEST AO The Low Oil Pressure RTT Warning Indicator Is Never Or Always On (2.0L EcoBoost) Refer to Wiring Diagrams for schematic and connector information. Normal Operation and Fault Conditions See Low Oil Pressure RTT Warning Indicator. If the engine rpm data or oil pressure warning message is missing less than 5 seconds, the IPC defaults the low oil pressure warning RTT indicator to the last state (on or off), based upon the last message received. If the engine rpm data or oil pressure warning message is missing for 5 seconds or longer, the IPC defaults the low oil pressure warning RTT indicator on. DTC Chart - PCM DTC Description Fault Trigger Conditions P0521 Engine Oil Pressure Sensor/Switch "A" Circuit Range/Performance Sets in the PCM when the PCM detects signal variation outside of the module parameters on the hardwired input from the oil pressure switch. P0522 Engine Oil Pressure Sensor/Switch "A" Circuit Low Sets in the PCM when the PCM detects a short to ground on the hardwired input from the oil pressure switch. P0523 Engine Oil Pressure Sensor/Switch "A" Circuit High Sets in the PCM when the PCM detects an open on the hardwired input from the oil pressure switch. P0524 Engine Oil Pressure Too Low Sets in the PCM when the PCM detects low oil pressure. Possible Sources Wiring, terminals or connectors Tachometer concern Message center concern Engine oil pressure switch Engine oil pressure concern GWM concern PCM concern IPC Visual Inspection and Diagnostic Pre-checks Inspect the: engine for noise or other symptom indicating a base engine or low engine oil pressure concern. engine oil pressure switch for signs of external damage. engine oil pressure switch connector for signs of corrosion harness for damage indicating an open or short to ground. PINPOINT TEST AO: THE LOW OIL PRESSURE RTT (RECONFIGURABLE TELLTALE) WARNING INDICATOR IS NEVER OR ALWAYS ON (2.0L EcoBoost ENGINE) AO1 CHECK THE MESSAGE CENTER OPERATION Ignition ON. Close all doors, the hood and the liftgate. Clear all message center warnings by pressing the OK button for each warning present. Monitor the door ajar RTT warning indicator. Open the driver door. Clear the message center popup warning. Monitor the door ajar RTT warning indicator. Is the door ajar RTT warning indicator off with the door closed, and on with the door open? Yes GO to AO2 No VIN required to access Guided Routine (IPC) AO2 CHECK THE GWM (GATEWAY MODULE A) DIAGNOSTIC TROUBLE CODES (DTCS) Using a diagnostic scan tool, check the GWM Continuous Memory Diagnostic Trouble Codes (CMDTCs). Are any Diagnostic Trouble Codes (DTCs) recorded? Yes REFER to: Communications Network (418-00 Module Communications Network, Diagnosis and Testing). No GO to AO3 AO3 CHECK THE TACHOMETER OPERATION Start the engine. NOTE: For the optional dual 4.2" message center display IPC , make sure the IPC is set to display the tachometer. The IPC and message center navigation can be found in the Owner's Literature Verify the tachometer operates. Does the tachometer operate? Yes GO to AO4 No For the optional IPC , GO to Pinpoint Test B For the base IPC , GO to Pinpoint Test H AO4 PERFORM THE IPC (INSTRUMENT PANEL CLUSTER) SELF-TEST Using a diagnostic scan tool, perform the IPC self-test. Are any Diagnostic Trouble Codes (DTCs) recorded? Yes REFER to DTC Chart: IPC in this section. No GO to AO5 AO5 CHECK THE OIL PRESSURE Test the engine for low oil pressure. Was a low oil pressure concern detected? Yes REPAIR the low oil pressure concern. REFER to: Engine (303-00 Engine System - General Information, Diagnosis and Testing). No GO to AO6 AO6 CHECK FOR VOLTAGE AT THE OIL PRESSURE SWITCH Ignition OFF. Disconnect Engine Oil Pressure Switch C1657 (2.0L). Ignition ON. Measure: 2.0L Engine Positive Lead Measurement / Action Negative Lead C1657 Pin 3 C1657 Pin 2 Is the voltage approximately 5 volts? Yes GO to AO7 No GO to AO10 AO7 CHECK THE OIL PRESSURE SENSOR SIGNAL CIRCUIT FOR A SHORT TO VOLTAGE Ignition OFF. Disconnect PCM C1381B (2.0L Engine). Ignition ON. Measure: 2.0L Engine Positive Lead Measurement / Action Negative Lead C1381B Pin 70 Ground Is any voltage present? Yes REPAIR the circuit. No GO to AO8 AO8 CHECK THE OIL PRESSURE SENSOR SIGNAL CIRCUIT FOR AN OPEN Ignition OFF. Measure: 2.0L Engine Positive Lead Measurement / Action Negative Lead C1381B Pin 70 C1657 Pin 1 Is the resistance less than 3 ohms? Yes GO to AO9 No REPAIR the circuit. AO9 CHECK THE OIL PRESSURE SENSOR SIGNAL CIRCUIT FOR A SHORT TO GROUND Measure: 2.0L Engine Positive Lead Measurement / Action Negative Lead C1657 Pin 1 Ground Is the resistance greater than 10,000 ohms? Yes GO to AO14 No REPAIR the circuit. AO10 CHECK THE OIL PRESSURE SENSOR VREF CIRCUIT FOR A SHORT TO VOLTAGE Ignition OFF. Disconnect PCM C1381B (2.0L Engine). Ignition ON. Measure: 2.0L Engine Positive Lead Measurement / Action Negative Lead C1657 Pin 3 Ground Is any voltage present? Yes REPAIR the circuit. No GO to AO11 AO11 CHECK THE OIL PRESSURE SENSOR VREF CIRCUIT FOR AN OPEN Ignition OFF. Measure: 2.0L Engine Positive Lead Measurement / Action Negative Lead C1657 Pin 3 C1381E Pin 6 Is the resistance less than 3 ohms? Yes GO to AO12 No REPAIR the circuit. AO12 CHECK THE OIL PRESSURE SENSOR VREF CIRCUIT FOR A SHORT TO GROUND Measure: 2.0L Engine Positive Lead Measurement / Action Negative Lead C1657 Pin 3 Ground Is the resistance greater than 10,000 ohms? Yes GO to AO13 No REPAIR the circuit. AO13 CHECK THE OIL PRESSURE SENSOR RETURN CIRCUIT FOR AN OPEN Measure: 2.0L Engine Positive Lead Measurement / Action Negative Lead C1657 Pin 2 C1381E Pin 20 Is the resistance less than 3 ohms? Yes INSTALL a new engine oil pressure sensor. REFER to: Engine Oil Pressure (EOP) Sensor (303-14A Electronic Engine Controls - 2.0L EcoBoost (184kW/250PS) – MI4, Removal and Installation). CLEAR the Diagnostic Trouble Codes (DTCs). TEST the system for normal operation. If the oil pressure RTT is still never or always on, GO to AO14 No REPAIR the circuit. AO14 CHECK FOR CORRECT PCM (POWERTRAIN CONTROL MODULE) OPERATION Ignition OFF. Disconnect and inspect the PCM and all related in-line connectors. Repair: corrosion (install new connector or terminals - clean module pins) damaged or bent pins - install new terminals/pins pushed-out pins - install new pins as necessary Reconnect the PCM and all related in-line connectors. Make sure they seat and latch correctly. Operate the system and determine if the concern is still present Is the concern still present? Yes CHECK On-Line Automotive Service Information System (OASIS) for any applicable Technical Service Bulletins (TSBs). If a TSB exists for this concern, DISCONTINUE this test and FOLLOW TSB instructions. If no Technical Service Bulletins (TSBs) address this concern, INSTALL a new PCM. Refer to the appropriate Removal and Installation procedure in Section 303-14. No The system is operating correctly at this time. The concern may have been caused by module connections. ADDRESS the root cause of any connector or pin issues. Diagnostic Pinpoint Test AO Supporting Documents Engine Oil Pressure (EOP) Sensor - Wiring Diagram - 2.0L EcoBoost - 2015 Edge.pdfPOWERTRAIN CONTROL MODULE (PCM) - Connector C1381B Details - 2.0L EcoBoost - 2015 Edge.pdf POWERTRAIN CONTROL MODULE (PCM) - Connector C1381B Location - 2.0L EcoBoost - 2015 Edge.pdf Oil Pressure Control Solenoid - Wiring Diagram - 2.0L EcoBoost - 2015 Edge.pdf POWERTRAIN CONTROL MODULE (PCM) - Connector C1381E Details - 2.0L EcoBoost - 2015 Edge.pdf POWERTRAIN CONTROL MODULE (PCM) - Connector C1381E Location - 2.0L EcoBoost - 2015 Edge.pdf Powertrain Control Module (PCM) - Removal and Installation - 2.0L EcoBoost - 2015 Edge Workshop Manual.pdf Good luck! -
Two terminal versus three terminal oil pressure switch/ sensor
Haz replied to JayMarks40's topic in 2015 Edge & MKX
Welcome to the Forum, @JayMarks40 ! From the 2015 Edge Workshop Manual... Engine Overview - 2.0L EcoBoost - 2015 Edge Workshop Manual.pdf Engine Specifications - 2.0L EcoBoost - 2015 Edge Workshop Manual.pdf Engine Oil Pressure (EOP) Sensor - Removal and Installation - 2.0L EcoBoost - 2015 Edge Workshop Manual.pdf Engine Oil Pressure (EOP) Sensor - Connector C1657 Location - 2.0L EcoBoost - 2015 Edge.pdf Engine Oil Pressure (EOP) Sensor - Connector C1657 Details - 2.0L EcoBoost - 2015 Edge.pdf Oil Pressure Control Solenoid - Removal and Installation - 2.0L EcoBoost - 2015 Edge Workshop Manual.pdf Oil Pressure Control Solenoid - Connector C1924 Location - 2.0L EcoBoost - 2015 Edge.pdf Oil Pressure Control Solenoid - Connector C1924 Details - 2.0L EcoBoost - 2015 Edge.pdf Good luck! -
From Unifor's website... Unifor extremely disappointed in Ford Motor Company decision to delay Oakville transition APRIL 4, 2024 TORONTO—Unifor calls on Ford Motor Company to consider all possible options to mitigate the negative impact on workers following the announced substantial delay in the launch of EV production at the Oakville Assembly Plant. “Unifor is extremely disappointed by the company’s decision. Our members have done nothing but build best-in-class vehicles for Ford Motor Company and they deserve certainty in the company’s future production plans,” said Unifor National President Lana Payne. “I want to be very clear here. Our members can be assured that we will push the company to explore every single possible opportunity to lessen the impact of this decision on them and their families.” Ford has announced that while the retooling of Oakville Assembly Plant will commence this Spring as planned, the company is delaying the launch of EV production from 2025 to 2027. Unifor was informed of the revised timeline during a meeting with Ford executives earlier this week. Unifor represents more than 5,600 Ford Canada workers, including 3,200 Local 707 members employed at the Oakville Assembly Plant. In 2020, Ford announced an historic $1.8 billion investment to retool the Oakville Plant for EV and battery pack production. In 2023 contract negotiations with Ford, Unifor negotiated innovative income and benefit transition supports, covering members at the Oakville plant for what was originally forecasted to be an eight-month retooling period. Negotiations included a provision that should the retooling period extend beyond eight months the company and the union will meet to discuss extending this arrangement. “There will be unexpected setbacks in the transition to EV, but we fully expect Ford to investigate every available option to support our Oakville members. It is unacceptable, after 120 years of operation in this country, that Ford does not plan to build a single vehicle in Canada for years on end,” said Local 707 Oakville Assembly Complex Chairperson Marc Brennan. Given the magnitude of the delay Unifor has requested a meeting with Ford to be held as soon as possible to discuss job and income security measures for workers. Ford Edge production at Oakville Assembly is scheduled to end in approximately one month. “This is a significant setback and while the first stages of retooling are still on track and we remain committed to securing an EV future for the workers of Oakville, the immediate challenges faced by our members will be front and centre in our discussions with the company,” Payne added. Unifor is Canada's largest union in the private sector and represents 315,000 workers in every major area of the economy. The union advocates for all working people and their rights, fights for equality and social justice in Canada and abroad, and strives to create progressive change for a better future.
-
These recent discussions may be helpful to you... Edge ST with performance brakes spare tire originated by @taurussvt Performance brake and tire package originated by @STBEAST Good luck!
-
SYNC 3 navigation offers maps for North Africa and South Africa, however SYNC 2 navigation may not be available. You might try telephoning the South Africa Ford Customer Relationship Center (CRC) , or e-mail the below CRC that best describes your region of Africa... South Africa 0860011022 fordcrc2@ford.com Sub-Saharan Africa ssacrc@ford.com North Africa nafcrc@ford.com Good luck!
-
For your subject matter research and Model Year comparisons... Instrument Panel Cluster (IPC) -Description and Operation - 2011 Edge-MKX Workshop Manual.pdf INSTRUMENT PANEL CLUSTER (IPC) - Connector C220 Pin-to-Circuit Details - 2011 Edge-MKX.pdf Instrument Panel Cluster (IPC) - Removal and Installation - 2011 MKX Workshop Manual.pdf Instrument Panel Cluster - Removal and Installation - Enhanced Image - 2011 Edge.pdf Instrument Panel Cluster - Removal and Installation - Enhanced Image - 2011 MKX.pdf Instrument Panel Cluster (IPC) - As-Built Configuration - 2011 MKX.pdf Instrument Panel Cluster (IPC) - Overview - 2016 MKX Workshop Manual.pdf Instrument Panel Cluster (IPC) - System Operation and Component Description - 2016 MKX Workshop Manual.pdf INSTRUMENT PANEL CLUSTER (IPC) - Connector C220 Pin-to-Circuit Details - 2016 MKX.pdf Instrument Panel Cluster (IPC) - Removal and Installation - 2016 MKX Workshop Manual.pdf Instrument Panel Cluster (IPC) - As-Built Configuration - 2016 MKX Select.pdf Instrument Panel Cluster (IPC) - Overview - 2022-2023 Nautilus Workshop Manual.pdf Instrument Panel Cluster (IPC) - System Operation and Component Description - 2022-2023 Nautilus Workshop Manual.pdf INSTRUMENT PANEL CLUSTER (IPC) - Connector C220 Pin-to-Circuit Details - 2022-2023 Nautilus.pdf Instrument Panel Cluster (IPC) - As-Built Configuration - 2022 Nautilus Standard.pdf Good luck!
-
SSM 52402 - 2024 Nautilus - Keyless Entry Keypad Illumination On 2024 Nautilus vehicles, the keyless entry keypad will only illuminate if the unlock button on the keyfob is pressed or if the keypad itself is touched. The keypad will not illuminate during approach detection or from any other inputs. Do not attempt repairs or submit a claim for this normal condition.
-
Wireless Accessory Charging Module (WACM) documents attached below... Wireless Accessory Charging Module (WACM) - Overview - 2020 Edge Workshop Manual.pdf Wireless Accessory Charging Module (WACM) - System Operation and Component Description - 2020 Edge Workshop Manual.pdf Wireless Accessory Charging Module (WACM) - Removal and Installation - 2020 Edge Workshop Manual.pdf Wireless Accessory Charging Module (WACM) - Diagnosis and Testing - 2020 Edge Workshop Manual.pdf Wireless Accessory Charging Module (WACM) - Grounds - Wiring Diagram - 2020 Edge.pdf Wireless Accessory Charging Module (WACM) - Power Distribution #1 - Wiring Diagram - 2020 Edge.pdf Wireless Accessory Charging Module (WACM) - Power Distribution #2 - Wiring Diagram - 2020 Edge.pdf Wireless Accessory Charging Module (WACM) - Module Communications #1 - Wiring Diagram - 2020 Edge.pdf Wireless Accessory Charging Module (WACM) - Module Communications #2 - Wiring Diagram - 2020 Edge.pdf Wireless Accessory Charging Module (WACM) - Wiring Diagram - 2020 Edge.pdf Wireless Accessory Charging Module (WACM) - Connector C390 Details - 2020 Edge.pdf Wireless Accessory Charging Module (WACM) - Connector C390 Location - 2020 Edge.pdf Good luck!
-
As the Workshop Manual image shows, the removable Upper Instrument Panel Storage Bin is retained by six clips and two screws... The 2017 Edge Wiring Diagrams offer several views of Instrument Panel and Heater/Evaporator Core Housing harnesses... Clearances between the floor of the Upper Instrument Panel Storage Bin and the various wiring harnesses & Heater/Evaporator Core Housing are unclear. Removing the Storage Bin involves disassembling several trim pieces and center stack components using procedures described in the below-attached documents... Front Controls Interface Module (FCIM) - Removal and Installation - With Touchscreen - 2017 Edge Workshop Manual.pdf Front Controls Interface Module (FCIM) - Removal and Installation - Sony Audio System - 2017 Edge Workshop Manual.pdf Center Registers - Removal and Installation - 2017 Edge Workshop Manual.pdf Instrument Panel Storage Bin – Removal (Task-specific edited from 2017 Edge Workshop Manual resource).pdf Heater Core and Evaporator Core Housing (For Imagery) - Removal and Installation - 2017 Edge Workshop Manual.pdf Instrument Panel Wiring Diagram - Interior View - 2017 Edge.pdf Instrument Panel Wiring Diagram - From Firewall View - 2017 Edge.pdf Climate Control Housing and Wiring Diagram - Firewall View - 2017 Edge.pdf When faced with where to place a Galaxy CB radio in our previous MKX, I elected to mount the bracket on the driver's door panel storage bin... Outboard leg room was diminished a bit, but the radio's controls were visible & usable when driving, and being black-on-black, the radio wasn't obvious when looking in from outside the vehicle. Good luck!
-
SSM 52393 2024 Nautilus - Predelivery Removal Tips For Exterior Shipping Protection (RapGard) Some 2024 Nautilus vehicles may exhibit difficulty removing shipping door protectors or white RapGard during predelivery. This may be attributed to varied environmental conditions during transit from the assembly plant to the dealerships. If possible, bring the vehicle into the shop to warm up and stabilize to a room temperature closer to 20°C (68°F) or higher prior to removing the plastic coverings. Running the engine may help in warming the hood wrapping adhesive for easier removal. Also, reuse the white RapGard that was removed from the car to dab/remove any adhesive residue left behind. For general guidelines, refer to the Warranty and Policy Manual, Section 2.9.00 Storage of New Vehicles. It's worth noting that in recent years, other automotive manufacturers have experienced paint defects caused by water migration beneath RapGard protective film. While differences exist between manufacturers' RapGard application methods, paint formulations, and vehicle sheltering during transit, it may be prudent for prospective 2024 Nautilus buyers to inspect the vehicle's paint to ensure defects like those pictured in the below-attached Volkswagen Technical Service Bulletin are not present. Volkswagen TSB 00-19-01 - Paint Defect - Water Migration Under the RapGard - 01-30-2023.pdf