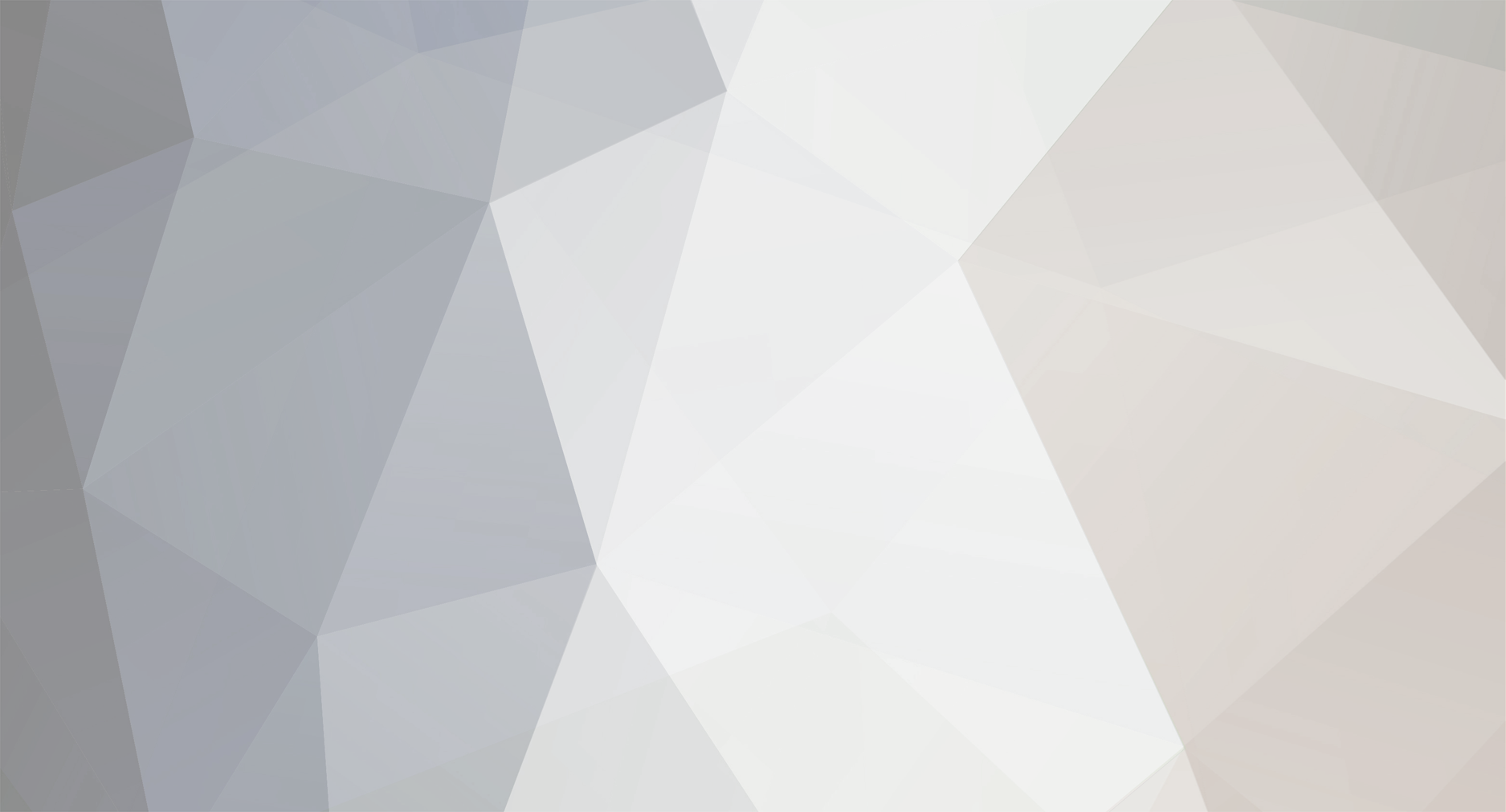

Haz
Edge Member-
Posts
1,194 -
Joined
-
Last visited
-
Days Won
304
Content Type
Profiles
Forums
Gallery
Everything posted by Haz
-
The scope of the Dealer Software Support Hotline is being expanded to responding to 2021 & 2022 and 2023 & 2024 Model Year vehicles with SYNC-related concerns. The Hotline will also serve as a resource to technicians experiencing challenges with Customer Satisfaction Program 24B47.
- 1 reply
-
- 2
-
-
The referred-to Special Service Message 52704 was previously posted to the Forum in relation to establishment of the Dealer Software Support (DSSH) Hotline... SSM 52704 2019-2024 Various Vehicles - SYNC 3 - Accessory Protocol Interface Module (APIM) Programming Error - "INSTL_ERR12" Using FDRS Or Stuck On "Updating System Software" Or No Response From The Vehicle When Using The Universal USB Updater Some 2019-2024 vehicles equipped with SYNC 3 may experience a programming Error - "INSTL_ERR12" while programming APIM using the Ford Diagnosis and Repair System (FDRS) or experience a frozen screen which says "updating system software" or no progress/response from module using the universal USB updater. This may be due to low memory in the APIM commonly occurring on software level NU5T-14G381-AB/BB. The current software level can be verified in the SYNC tab of Professional Technician System (PTS) or using the vehicle's center display screen, Settings > General > About. To correct the condition, run the universal USB updater. If unsuccessful, using the latest software version of the FDRS scan tool, run the service function "APIM - Reset the Accessory Protocol Interface Module Application" and select "Clear All User Data" option. The center display screen will reboot. As soon as the vehicle's center display screen displays the boot up logo, immediately reinsert the same universal serial bus (USB) drive that was utilized during the prior failed programming attempt. The vehicle's center display screen should display "successful APIM update" when complete. If process does not complete as expected, retry no more than one time. If the concern persists, then raise a Technical Support Request for assistance. Do not replace the APIM prior to contacting Technical Support.
-
Welcome to the Forum @Mystifyu! 2015 Edge Blower Motor resources are attached below as PDF documents... Good luck! Blower Motor - Removal and Installation - 2015 Edge Workshop Manual.pdf Blower Motor Speed Control - Removal and Installation - 2015 Edge Workshop Manual.pdf Climate Control System - Vehicles With DATC - System Operation and Component Description - 2015 Edge Workshop Manual.pdf Blower Motor - Wiring Diagram - 2015 Edge.pdf Battery Junction Box (BJB) - Illustration Showing Blower Motor Relay Location - 2015 Edge.pdf Battery Junction Box (BJB) - Illustration Showing Location - 2015 Edge.pdf
-
SSM 52730 - 2023-2024 F-Super Duty And 2024 F-150/Nautilus - Diagnostic Trouble Code (DTC) U211B:51 Stored In The TCU After Software Update Or An OTA Some 2023-2024 F-Super Duty and 2024 F-150/Nautilus vehicles may set DTC U211B:51 in the telematics control unit (TCU) module after a software update on the TCU is performed at dealer or via over the air (OTA) Update. The DTC U211B:51 in the TCU has no effect on vehicle functionality or connectivity. Replacement or reprogramming of the TCU will not resolve this condition. DTC U211B:51 should be ignored if no other DTCs are present in the TCU and no symptoms present. No further service action is required.
-
@eric1: You are correct that in the text you quoted, I should've included the word 'valve" after "EGR" to be consistent with that previously attached "Exhaust Gas Recirculation (EGR) Valve" Workshop Manual section... I regret that my omission of the word "valve" unnecessarily lengthened your path toward resolving your Edge's issue. Good luck!
-
SSM 52729 - 2022-2024 Ford Edge ST - AWD - 2.7L - Adaptive Cruise Control (ACC) - Cruise Control Deactivates With Illuminated ABS Light And Various Brake And Driver-Assist Warning Indicators, DTCs U3000:49 Stored In The ABS And U0415 In The PSCM Some 2022-2024 Ford Edge ST vehicles equipped with all wheel drive (AWD), a 2.7L engine, and ACC may exhibit cruise control deactivating with an illuminated anti-lock brake system (ABS) warning light flashing and various brake and driver-assist warning indicators. Diagnostic trouble codes (DTCs) U3000:49 may be stored in the ABS module with U0415 in the power steering control module (PSCM). This may be due to the software in the ABS module. To correct this condition, reprogram the ABS module using the latest level of the Ford Diagnosis and Repair System (FDRS) tool. Refer to the Workshop Manual (WSM), Section 206-09 Anti-Lock Brake System. For claiming use the causal part number 2C219 and applicable labor operations in Section 2 of the Service Labor Time Standards (SLTS) Manual.
-
It's in the software -- "all-wheel-drive calibration for balanced front and rear torque distribution" -- as shared in your January 2024 discussion on this same topic... Good luck!
-
SSM 52727 2024 Ranger/Nautilus - Inoperative Global Opening/Closing Feature Some 2024 Ranger/Nautilus vehicles may exhibit an inoperative global opening/closing feature. Refer to the Workshop Manual (WSM), Section 501-11 for normal diagnostics. If normal diagnostics do not resolve the issue, inform the customer that Ford is currently working on a solution for this condition. Monitor OASIS for additional information and schedule service appointments for customers once the repair becomes available. Feature description from 2024 Nautilus Workshop Manual... Global Opening /Closing The remote control can be used to operate the windows when the ignition is off and the accessory delay feature is not active. Within a short time after unlocking the vehicle doors with the remote control transmitter, press and hold the unlock button on the remote control transmitter until the windows begin opening. The windows automatically open. To close the windows. Within a short time after locking the vehicle doors with the remote control transmitter, press and hold the lock button on the remote control transmitter until the windows begin closing. The windows automatically close. Pressing the lock or unlock button while the windows are moving (in either direction) stops window movement. This feature can be enable or disable via the touchscreen. For information regarding this feature, refer to the Owner's Literature. The content can be found in the Windows section. Attached below as PDF documents are the above-mentioned normal diagnostic procedures... Power Door Window Initialization - General Procedure - 2024 Nautilus Workshop Manual.pdf Diagnostic Pinpoint Test I - The Global Open-Close Function Is Inoperative - 2024 Nautilus Workshop Manual.pdf Driver & Passenger Door Modules - Wiring Diagram 100 - 2024 Nautilus.pdf
-
SSM 52722 - 2019–2024 Ford And Lincoln Vehicles - Equipped With SYNC3 - Various FordPass/LincolnWay Connectivity Concerns With DTC B156D:89 Stored The Telematics Control Unit Module (TCU) Some 2019-2024 Ford and Lincoln vehicles equipped with SYNC3 may experience various FordPass/LincolnWay connectivity concerns including but not limited to: missing activation prompt (pop-up) on the vehicle's center display screen when attempting to activate vehicle through FordPass/LincolnWay, incorrect location/global positioning system (GPS) reported through FordPass/LincolnWay, problems with remote commands being performed through FordPass/LincolnWay, incorrect data/information reported on FordPass/LincolnWay. These symptoms will be accompanied by diagnostic trouble code (DTC) B156D:89 in the TCU. This may be due the accessory protocol interface module (APIM) software. To correct the condition, update the APIM software.
-
With emphasis added... SSM 52724 - 2024 Nautilus, 2025 Explorer/Police Interceptor Utility - Right (Passenger) Exterior Mirror Does Not Unfold After The Vehicle Is Unlocked Some 2024 Nautilus and 2025 Explorer/Police Interceptor Utility vehicles may exhibit a symptom where the vehicle's right (passenger) exterior mirror does not come out of the folded position after the vehicle is unlocked. This may be due to a software concern within the driver's door module (DDM) and passenger's door module (PDM). If the mirror unfolds after pressing the mirror fold button in the vehicle twice, inform customers that they can continue to drive the vehicle and engineering is currently working on a solution for this condition that is expected in Q4 2024. Replacement or reprogramming of the DDM and PDM will not resolve this condition at this time. Monitor OASIS for additional information and schedule service appointments for customers once the repair becomes available. If the mirror does not unfold after pressing the mirror fold button in the vehicle twice, refer to Workshop Manual (WSM), Section 501-09 for further diagnostics.
-
Parking Sensor Wiring Diagrams 2019-2024
Haz replied to Wubster100's topic in Accessories & Modifications
Additional... Good luck! Parking Aid - Active Park Assist System Operation and Component Description - 2021 Edge Workshop Manual.pdf Parking Aid - Active Park Assist Overview - 2021 Edge Workshop Manual.pdf Parking Aid - Active Park Assist Component Location - 2021 Edge Workshop Manual.pdf Parking Aid - Active Park Assist Azimuth System Check - 2021 Edge Workshop Manual.pdf Parking Aid - Front Active Park Assist Sensors - Removal and Installation - 2021 Edge Workshop Manual.pdf Parking Aid - Rear Active Park Assist Sensors - Removal and Installation - 2021 Edge Workshop Manual.pdf Rear Bumper Cover - Removal and Installation - 2021 Edge Workshop Manual.pdf Parking Aid - Active Park Assist - Diagnosis and Testing - 2021 Edge Workshop Manual.pdf -
Parking Sensor Wiring Diagrams 2019-2024
Haz replied to Wubster100's topic in Accessories & Modifications
Body Control Module (BCM) connector information and Parking Aid/Active Park Assist operational information attached below as PDF documents... BODY CONTROL MODULE (BCM) - Connector C2280G Pins-Circuits Detail - 2021 Edge.pdf BODY CONTROL MODULE (BCM) - Connector C2280G Location - 2021 Edge.pdf BODY CONTROL MODULE (BCM) - Connector C2280E Pins-Circuits Detail - 2021 Edge.pdf BODY CONTROL MODULE (BCM) - Connector C2280E Location - 2021 Edge.pdf BODY CONTROL MODULE (BCM) - Connector C2280C Pins-Circuits Detail - 2021 Edge.pdf BODY CONTROL MODULE (BCM) - Connector C2280C Location - 2021 Edge.pdf BODY CONTROL MODULE (BCM) - Illustration Showing Connector Locations - 2021 Edge.pdf BODY CONTROL MODULE (BCM) - Fuses-Circuits Legend - 2021 Edge.pdf -
Based upon your observations, the following 2020 Edge Workshop Manual sections may be helpful... Good luck! Air Conditioning Odor Treatment - General Procedures - 2020 Edge Workshop Manual.pdf A-C Odor Remover Flexible Applicator - Rotunda 258-62644 - AirSept - YN-29 Applicator.pdf Blower Motor Speed Control - Removal and Installation - 2020 Edge Workshop Manual.pdf Cabin Air Filter - Removal and Installation - 2020 Edge Workshop Manual.pdf Climate Control System - Dual Automatic Temperature Control (DATC) - Component Location - 2020 Edge Workshop Manual.pdf Cowl Panel Grille - Removal and Installation - 2020 Edge Workshop Manual.pdf Windshield Wiper Pivot Arm - Removal and Installation - 2020 Edge Workshop Manual.pdf Air Inlet Door Actuator - Removal and Installation - 2020 Edge Workshop Manual.pdf
-
2018 Edge titanium rear window washer
Haz replied to Gardenman's topic in 2019-2020 Edge & Nautilius
@Gardenman: The information provided in @Rlahnan0121's recent discussion Rear washer fluid not spraying may be helpful to you. Good luck! -
Additional... UK Ford PowerShift Transmission Fluid Level Check - Supplemental Video Good luck! Transmission Fluid Level Check - 6-Speed PowerShift - 2015-2018 Edge Workshop Manual - U.K Edition.pdf Engine Cooling System - Coolant Hose - 2.0L EcoBlue Diesel - 2015-2022 Edge Workshop Manual - U.K Edition.pdf Engine Cooling System Draining, Vacuum Filling and Bleeding - 2.0L EcoBlue Diesel - 2015-2022 Edge Workshop Manual - U.K Edition.pdf Transmission Fluid Drain and Refill - 6-Speed PowerShift - 2015-2018 Edge Workshop Manual - U.K Edition.pdf Power Transfer Unit - Fluid Level Check - 2.0L EcoBlue Diesel - 2015-2022 Edge Workshop Manual - U.K Edition.pdf Engine - Component Location - 2.0L EcoBlue Diesel - 2015-2022 Edge Workshop Manual - U.K Edition.pdf Rear Differential - Fluid Level Check - 2.0L EcoBlue Diesel - 2015-2022 Edge Workshop Manual - U.K Edition.pdf Air Cleaner - Removal and Installation - 2.0L EcoBlue Diesel - 2015-2022 Edge Workshop Manual - U.K Edition.pdf All-Wheel Drive (AWD) Systems - Overview - 2.0L EcoBlue Diesel - 2015-2022 Edge Workshop Manual - U.K Edition.pdf Power Transfer Unit - Component Location - 2.0L EcoBlue Diesel - 2015-2022 Edge Workshop Manual - U.K Edition.pdf Engine Specifications - 2.0L EcoBlue Diesel - 2015-2022 Edge Workshop Manual - U.K Edition.pdf Transmission Specifications - 6-Speed PowerShift - 2015-2018 Edge Workshop Manual - U.K Edition.pdf
-
The U.K. Ford Owner Support website provides Service and Oil Change Intervals by submitting the vehicle VIN and current odometer reading. From the above-linked web page... When should I get my car serviced? Service intervals vary by vehicle model and engine type, but are specified in the Service Portfolio supplied with your vehicle and can also be found in our maintenance schedule portal. For further enquiries please contact your local Ford Dealer who is best placed to confirm the exact schedule for your vehicle and also advise of any recall or service actions that may be outstanding on your vehicle. For more information, check our Service & Repair pages. If you've already found that information lacking, hopefully, your dealer Service Department can provide you a Scheduled Maintenance interval guide. Ford offers subscriptions ($26.34 for 72-hours, $341.20 for 30-days, $2,834.95 for 1-year) for online access to the following information... It's worth noting that indicating the United Kingdom as your country on the initial landing page eliminates the subscription offer... As an alternative, attached below and in an immediately following post as PDF documents are U.K. procedures for the fluid maintenance you look forward to performing on your 2018 AWD 2.0L EcoBlue 6-Speed PowerShift Edge... Oil Pan - Removal and Installation - 2.0L EcoBlue Diesel - 2015-2022 Edge Workshop Manual - U.K Edition.pdf Engine - System Operation and Component Description - 2.0L EcoBlue Diesel - 2015-2022 Edge Workshop Manual - U.K Edition.pdf Power Transfer Unit - Overview - 2.0L EcoBlue Diesel - 2015-2022 Edge Workshop Manual - U.K Edition.pdf Engine Cooling System - Specifications - 2.0L EcoBlue Diesel - 2015-2022 Edge Workshop Manual - U.K Edition.pdf Power Transfer Unit - Fluid Specifications - 2.0L EcoBlue Diesel - 2015-2022 Edge Workshop Manual - U.K Edition.pdf Rear Differential - Fluid Specifications - 2.0L EcoBlue Diesel - 2015-2022 Edge Workshop Manual - U.K Edition.pdf
-
GENERAL SERVICE BULLETIN Various Vehicles - Exterior Lighting Concern Analysis 24-7068 09 July 2024 This bulletin supersedes 23-7106. Reason for update: revised Service Information Summary This article is designed to provide examples of exterior lamp conditions/damage to assist in determining if the condition is warrantable/non-warrantable. Refer to the latest version of the Warranty and Policy Manual for the latest exterior lamp warranty coverage. Use this article to assist in determining warrantable exterior lighting concerns. Service Information Exterior lamps are vented to allow accumulated water vapor to be expelled and accommodate normal changes in pressure inside the lamp. This vent system allows accumulated vapor to be expelled from the lamp over time. The vent system continuously operates even when the lamps are not powered on, however, it is most effective when the lamps are powered on and while the vehicle is in motion. A fine mist or white fog, frost, condensation on the interior side of the lamp lens can be a natural by-product of this vented design. This is normal during cold, wet (rain), damp (humid) conditions or after a carwash. The thin mist eventually clears and exits through the vents during normal operation. Normal condensation (non-warrantable) is defined by a fine mist or white fog, frost on the interior side of a lamp lens that may include small droplets of liquid up to 2mm in diameter. This condition is not time limited and is not warrantable if the criteria is met. Other Non-warrantable conditions: • Scratches/scrapes/cracks, etc. • Modifications • Paint transfer marks on the lamp assembly • Lamps/reflectors/attachments which are loose, cracked, or broken Water leak (warrantable) is defined by lamps that exhibit streaking and droplets of liquid larger than 2mm in diameter on the interior of the lens or pooling of water at the bottom of the lamp. Condensation is most prevalent during the fall and springtime. High humidity and substantial fluctuation in temperature between morning, day, and night can result in more moisture within the lamp. Clearing times are increased during the changing seasons. The time required to clear the condensation may vary drastically based on the size, shape, location of the lamp on the vehicle, amount of time the lamp is on, and the atmospheric conditions that the lamp is exposed to. Customers with short commutes will experience a longer time for the lamp to clear. A customer may explain "the fogging appears and disappears", this is normal. If a defect exists and wet/humid conditions continue, the lamp condition will escalate to a water leak as described above. For warranty repairs, use the lowest level service part rather than an assembly replacement. Such components may include mirror signal lenses and puddle lamps which are often serviced separately from the mirror assembly. Prior to warranty analysis, thoroughly clean and dry the outside surface of the lamp assembly. Aftermarket/Counterfeit Lamps Aftermarket lamps may be installed on a vehicle after collision damage repair. Aftermarket lamps tend to mimic the appearance of an original equipment manufacturer (OEM) lamp but often lack quality and performance of an OEM lamp. Aftermarket lamps are more prone to water leaks and operational malfunction. If a lamp is found to be aftermarket, it cannot be replaced under warranty. An original equipment Ford/Lincoln part will have the brand logo imprinted (Figure 1) in the lens and housing. Figure 1 Examples Of Normal Condensation (Figures 2-5) - Do Not Replace Under Warranty Figure 2 - not warrantable Figure 3 - not warrantable Figure 4 - not warrantable Figure 5 - not warrantable Examples Of Water Leaks (Figures 6-8) - Warrantable Figure 6 - example of water leak (large droplets) - warrantable Figure 7 - example of water leak (streaking) - warrantable Figure 8 - example of water leak (pooling at bottom) - warrantable Examples Of Other External Lighting Concerns (Figures 9-15) Figure 9 - example of parting line - not covered under warranty Figure 10 - example of modification (silicone) - not covered under warranty Figure 11 - example of external impact damage - not covered under warranty Figure 12 - example of modification (hole drilled) - not covered under warranty Figure 13 - example of peeling hard coat - warrantable Figure 14 - example of "crazing" - warrantable Figure 15 - example of distorted logo lamp - warrantable © 2024 Ford Motor Company All rights reserved. NOTE: This information is not intended to replace or supersede any warranty, parts and service policy, workshop manual (WSM) procedures or technical training or wiring diagram information.
-
Parking Sensor Wiring Diagrams 2019-2024
Haz replied to Wubster100's topic in Accessories & Modifications
Attached... Good luck! Parking Aid Wiring Diagram #1 - 2024 Edge.pdf Parking Aid Wiring Diagram #2 - 2024 Edge.pdf Parking Aid Wiring Diagram #3 - 2024 Edge.pdf Parking Aid Wiring Diagram #4 - 2024 Edge.pdf Parking Aid Wiring Diagram #5 - 2024 Edge.pdf Parking Aid Wiring Diagram #6 - 2024 Edge.pdf Parking Aid Wiring Diagram #7 - 2024 Edge.pdf Parking Aid Wiring Diagram #8 - 2024 Edge.pdf Rear Parking Aid Sensors - Wiring Harness Location - 2024 Edge.pdf Front Parking Aid Sensors - Wiring Harness Location - 2024 Edge.pdf Rear Parking Aid Camera - Wiring Harness Location - 2024 Edge.pdf Front Parking Aid Camera - Wiring Harness Location - 2024 Edge.pdf Rear Parking Aid Sensors - Inline Connector C438 - 2024 Edge.pdf Rear Parking Aid Sensors - Inline Connector C140 - 2024 Edge.pdf Active Park Assist Switch - Connector C3466 Location - 2024 Edge.pdf Active Park Assist Switch - Connector C3466 - 2024 Edge.pdf -
Body Control Module (BCM) Illustration & Connector Locations - 2024 Nautilus.pdf Body Control Module (BCM) & Connectors C2280A & C2280B Location - 2024 Nautilus.pdf Body Control Module (BCM) & Connectors C2280C & C2280D & C2280E Location - 2024 Nautilus.pdf Body Control Module (BCM) & Connector C2280F Location - 2024 Nautilus.pdf Body Control Module (BCM) - Removal and Installation - 2024 Nautilus Workshop Manual.pdf Body Control Module B (BCMB) & Connector C3347 Location - 2024 Nautilus.pdf Body Control Module B (BCMB) - Removal and Installation - 2024 Nautilus Workshop Manual.pdf
-
Fuses and Fuse Box Locations - 2024 Nautilus Owner's Manual.pdf Central Junction Box (CJB) - Fuse-Relay Locations - 2024 Nautilus.pdf Central Junction Box (CJB) - Fuses-Circuits Listing #1 - 2024 Nautilus.pdf Central Junction Box (CJB) - Fuses-Circuits Listing #2 - 2024 Nautilus.pdf Central Junction Box (CJB) - Fuses-Circuits Listing #3 - 2024 Nautilus.pdf Central Junction Box (CJB) - Connector C2281A & C2281B Locations - 2024 Nautilus.pdf Central Junction Box (CJB) & Connectors C2281A & C2281B Location - 2024 Nautilus.pdf Battery Junction Box (BCMC) & High Current Battery Junction Box (BJB) Illustration - 2024 Nautilus.pdf Battery Junction Box (BCMC) - Fuses-Circuits Listing #1 - 2024 Nautilus.pdf Battery Junction Box (BCMC) - Fuses-Circuits Listing #2 - 2024 Nautilus.pdf Battery Junction Box (BCMC) - Fuses-Circuits Listing #3 - 2024 Nautilus.pdf Battery Junction Box (BCMC) Illustration & Connectors C1035A & C1035B Location - 2024 Nautilus.pdf Battery Junction Box (BCMC) Illustration & Connectors C1035A & C1035B Location - 2024 Nautilus.pdf Low Voltage High Current Fuse - 2.0L EcoBoost - Removal and Installation - 2024 Nautilus Workshop Manual.pdf Battery Junction Box (BCMC)) - Removal and Installation - 2024 Nautilus Workshop Manual.pdf
-
Attached below as PDF documents are Adaptive Cruise Control sections from the 2022 Edge Workshop Manual... Good luck! Adaptive Cruise Control - System Operation and Component Description - 2022-2024 Edge Workshop Manual.pdf Module Configuration - System Operation and Component Description - 2022-2024 Edge Workshop Manual.pdf Cruise Control Radar Alignment - General Procedures - 2022-2024 Edge Workshop Manual.pdf Cruise Control Module (CCM) - Removal and Installation - 2022-2024 Edge Workshop Manual.pdf Front Bumper Cover - Removal and Installation - 2022-2024 Edge Workshop Manual.pdf
-
Welcome to the Forum, @SV101! Presumably, your dealer found evidence on the bumper cover and/or the Cruise Control Module (CCM) that the bracket breakage and ruined CCM was the result of a collision of some sort. Electronic modules that have been physically dropped are always to be replaced, so if the CCM suffered an impact sufficient to fracture its mounting bracket, then the CCM must be replaced. You are not being "ripped off". The following images describe the auto-braking feature your Edge's optional Co-Pilot 360 package provides... You may want to explore submitting a claim to have the repair cost paid under the collision coverage of your auto insurance. Good luck!
-
Customer Satisfaction 22N12- Flex Plate Crack on 2.0
Haz replied to All Hat No Cattle's topic in Recalls, TSBs & Warranty
The CSP-designated replacement flexplate (1S7Z-6375-D) is shown as replacing two previous flexplate part numbers (1L8Z-6375-AA and 1S7Z-6375-B). So, engineering improvement (EI) changes to the previous part numbers have likely occurred. Good luck! -
Just in case, interior mirror Workshop Manual section is attached below as a PDF document... Good luck! Interior Rear View Mirror - Removal and Installation - 2007 Edge Workshop Manual.pdf
-
Installing keyless entry keypad KB3Z-14A626-B
Haz replied to SandyT's topic in Alarms, Keyless Entry, Locks & Remote Start
Welcome to the Forum, @SandyT! 2020 to current Model Year - Wireless RF Key Pad Instructions are attached below as a PDF document... Per the instructions, KB3Z-14A626-B is for vehicles built with factory remote start. Good luck! Multiple Vehicle Lines - With Keyless Remote Entry System.pdf Wireless RF Key Pad Diagnosis Guide.pdf- 1 reply
-
- 2
-